In the presence of Safran CEO Olivier Andriès, Safran officially inaugurated its new Safran Blades facility in the province of Liège, Belgium. This state-of-the-art plant specializes in the production of titanium compressor blades, a critical component found by the hundreds in each aircraft engine.
Safran Blades: at the dawn of a new era.
“With Safran Blades, we are doing much more than opening a factory. We are taking a decisive lead – technologically, industrially, and environmentally. This project reflects our commitment to mastering our value chains while co-building, with our Belgian partners, a stronger, more innovative, and more sustainable European aeronautics industry,” said Olivier Andriès, CEO of Safran.

As part of Safran’s strategy to strengthen its autonomy and secure its supply chain, the Safran Blades facility is set to produce 700,000 titanium blades annually by 2026 – primarily for LEAP and GEnx engines powering Airbus and Boeing aircraft – equivalent to one blade every 20 seconds!
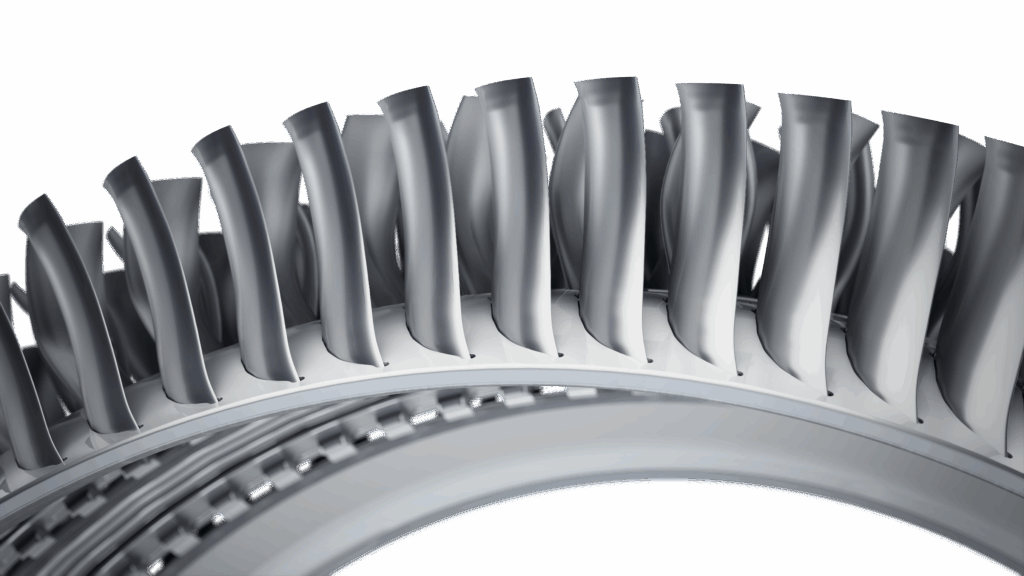
Image ©️Anthony Lemoine. Safran.
A new Factory 4.0
Built on a fully remediated former steel industry site, the new 10,000-m² center of excellence, certified “Factory of the Future 2025”, is a modern production model, designed to meet the highest international standards. The Factory 4.0 incorporates automation, robotics, connected objects, massive data collection and artificial intelligence, which optimizes production, costs, and the environmental footprint.

Strong synergies with the local ecosystem
To bring this digitalized factory to life, Safran relied on Belgian and European players, drawing on a dynamic industrial environment and cutting-edge local skills.
Walloon companies are the beating heart of Safran Blades
« We designed this next-generation plant in collaboration with innovative Walloon companies, » explains Mathieu Deladrière, CEO Safran Blades « It’s thanks to a robust and agile local ecosystem that we were able to bring this industrial activity to Wallonia!”
As part of the project, Safran is working closely with two research centres:
– CRM → focused on optimising forging dies with the objective of making them intelligent.
– Sirris → developing a real-time, non-contact inspection system using laser technology capable of recreating the measured blade in less than 20 seconds.
This scientific expertise is reinforced by the technological know-how of five cutting-edge companies:
ID – Desimone → took the lead in developing a standard production cell adaptable to various manufacturing processes, integrating diverse areas of expertise such as mechanics, automation, and specialized controls. In collaboration with Safran Blades, ID designed the plant’s “backbone” – a system capable of automatically derinding parts and performing inspection, marking, sorting, and laser cutting – all within a cycle time of under 20 seconds.
Indutec → developed a high-performance waterjet cutting machine offering very high precision, speed, and operational efficiency.

Smartyou → deploys the ‘MES’ system, a complete and autonomous production management IT solution. Acting as the true conductor of the workshop, it coordinates all operations in real time to ensure optimal workflow and industrial process fluidity.
Rovi-tech → is developing an automated decision-support tool and a non-destructive testing process. In collaboration with ID-Desimone, Rovi-tech is creating a tool that pre-selects parts during inspection, thereby facilitating the work of certified inspectors and enhancing the reliability of the process.
Finally, based on all the data collected, the Safran Blades team, together with Pepite, is developing an artificial intelligence capable of anticipating quality defects and adjusting tools in real time.
More than ever, Wallonia is determined to play a leading role in a fast-changing aeronautics industry, focusing on innovation, sustainability, and sovereignty.

Image©️Anthony Lemoine. Safran.
At the inauguration of the new plant, Adrien Dolimont, Minister-President of the Walloon Government, said:
« The creation of Safran Blades demonstrates our ability to realize an ambitious industrial project in our region within a remarkably short timeframe – just 24 months. For many years, the aerospace and defence sector has been a strategic pillar of Wallonia’s industrial development.
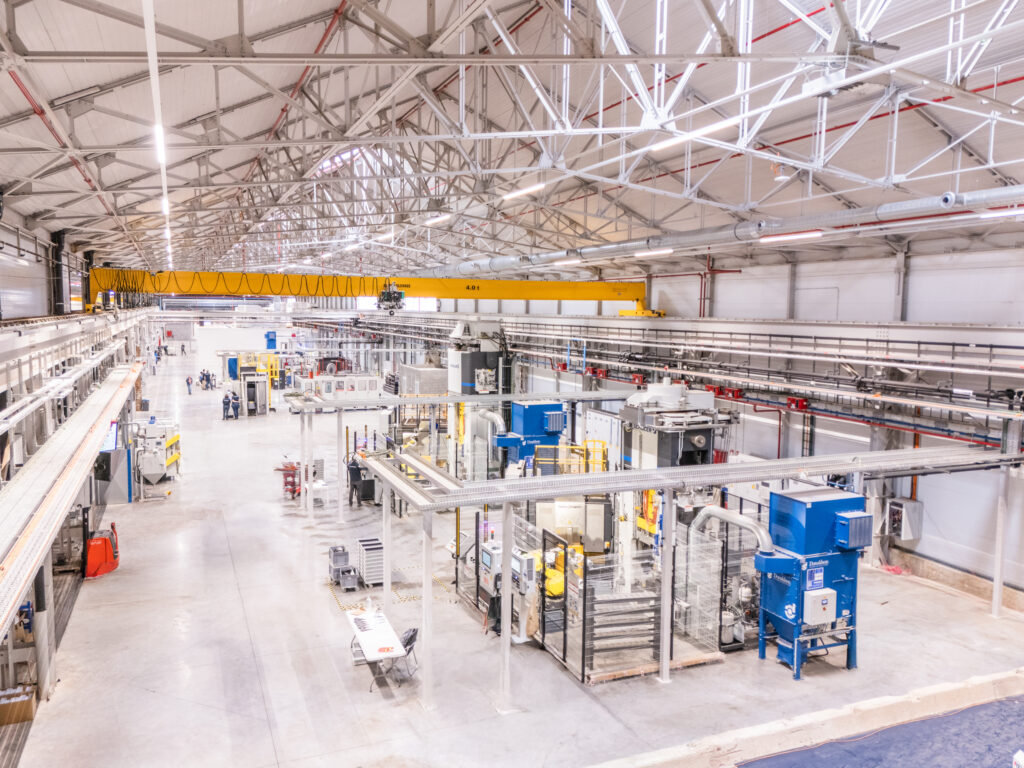
We are fortunate to have highly skilled universities, research centres, and industries that nurture this ecosystem. The WINGS project, launched at the end of 2020 and recently extended by the Walloon Region, is fully aligned with this dynamic: its aim is to stimulate research and technological development to maintain the sector’s competitiveness and give it the means to meet the major challenges of the ecological transition and decarbonisation”
Article & visual©️Gate.31